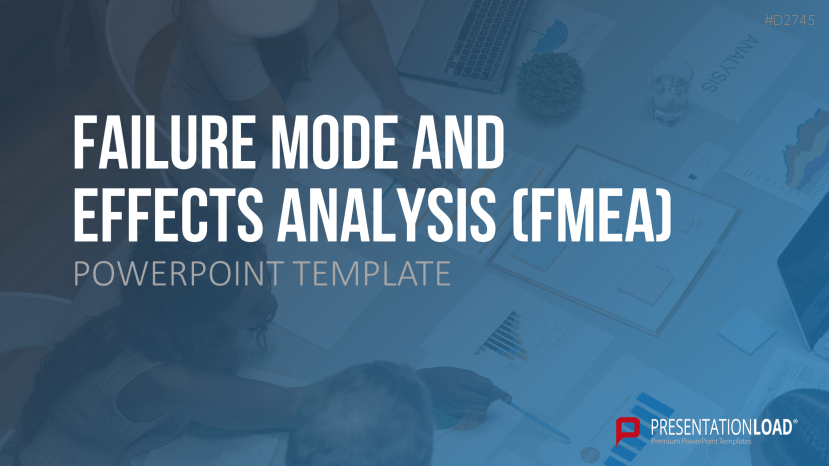
What is FMEA used for?
As part of quality management, FMEA helps keep an eye on the requirements of a company and its customers. In doing so, it increases competitiveness. The continuous improvement of products and/or services ensures that weak points can be identified and dealt with, both in existing processes and in new product launches.
A complete analysis in 7 steps
Thanks to its thorough 7-step system, FMEA can become part of any process -- from concept to finished product. This includes planning, structural analysis, functional analysis, failure analysis, activity analysis, optimization and finally, results documentation. Our detailed illustrations of the procedure facilitate its use.
New developments and their significance
Since June 2019, there have been some adjustments to the previous FMEA procedure. One of them is to replace the risk priority number (RPN), which evaluates the risk of occurrence, detection and severity of the failure. However, because RPN analysis is imprecise, it has been replaced by the more precise task priority (AP). This allows for a clear understanding of the urgency for action and prioritization of work. Use our numerous illustrations and forms to present these metrics professionally.
With the FMEA set for PowerPoint, you can
- use a guide to identify, evaluate, and avoid risks.
- stay up to date with the FMEA procedure.
- enjoy a wide range of visuals illustrating how potential failures can be identified and avoided.
This PowerPoint template includes:
- Core Concept and Definition:
- Meaning of the acronym
- Definition
- Types of FMEA
- Applications for product and process FMEA
- The rule of ten for failure costs (preventive quality assurance)
- FMEA facilitation
- Advantages and Goals:
- Examples
- Advantages of FMEA
- 7 Steps:
- Presentation options
- General approach
- Step 1: planning
- FMEA project planning with the 5T method
- Scope of analysis through degree of novelty
- Step 2: Structure analysis
- Boundary diagram
- Block diagram
- Step 3: Function analysis
- Structure tree
- Parameter diagram
- Ishikawa diagram
- Step 4: failure analysis
- 5 whys method
- Failure network
- Step 5: risk analysis
- Risk assessment
- Step 6: Optimization
- Measures
- Step 7: results documentation
- Points for documentation
- Risk Priority Number and Task Priority/Action Priority:
- Updates
- The problem with RPN
- Task priority instead of RPN
- AP logic table
- Values
- AP table
- FMEA variants
- Bow-tie analysis
- HAZOP: hazard and operability
- HACCP: hazard analysis critical control point
- FMEA FORM:
- Explanations
- FMEA form: variants
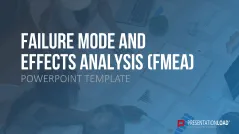
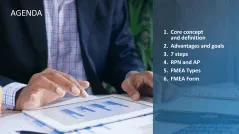
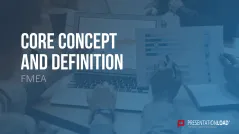
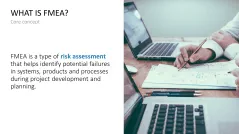
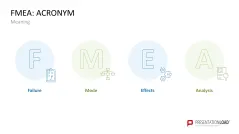
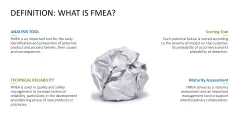
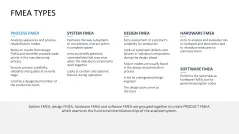
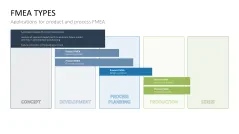
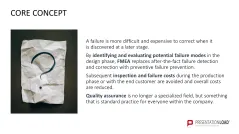
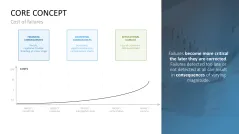
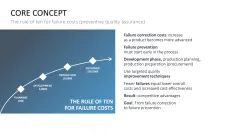
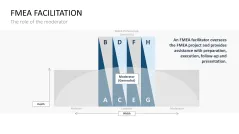
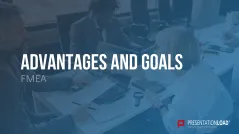
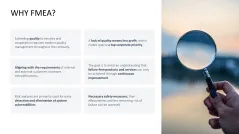
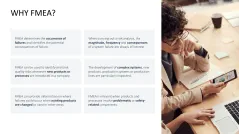
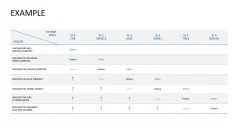
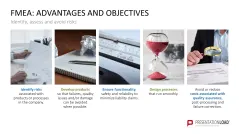
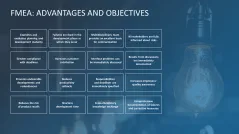
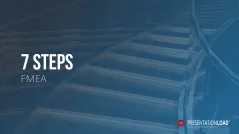
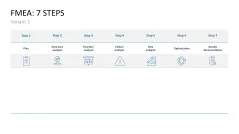
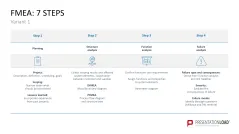
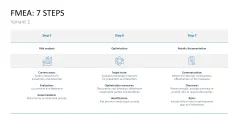
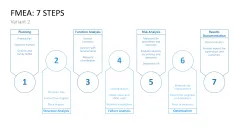
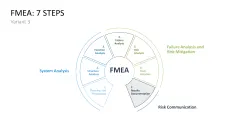
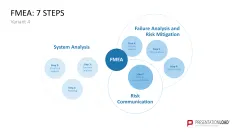
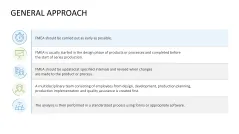
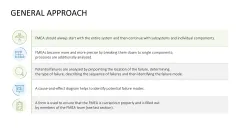
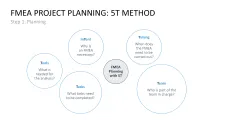

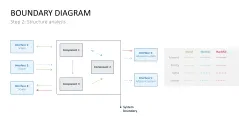
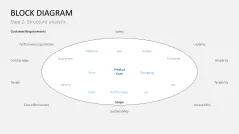
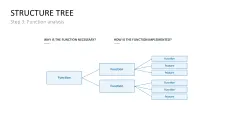
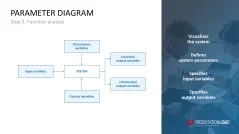

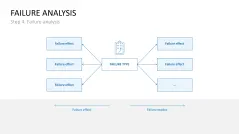
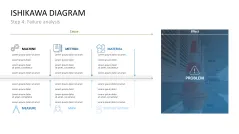
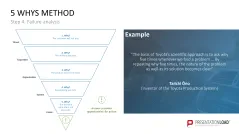
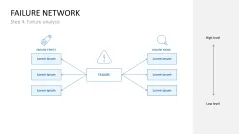
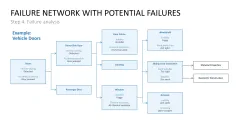
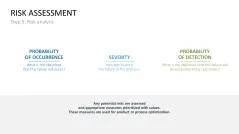
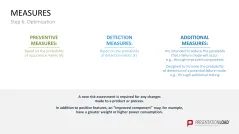
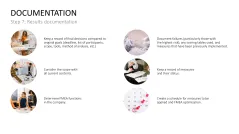
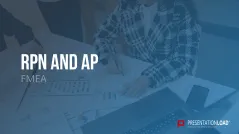
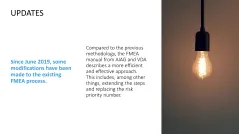
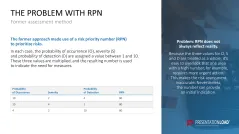
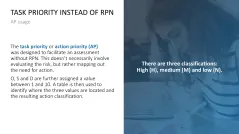
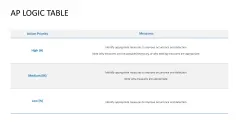
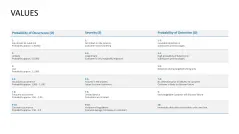
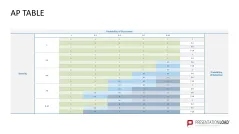
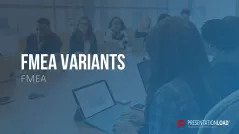
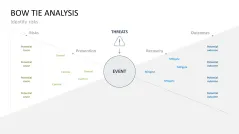
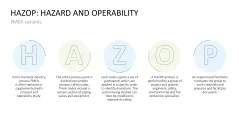
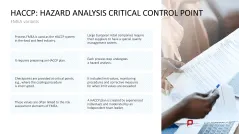
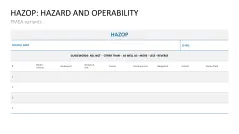
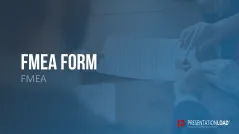
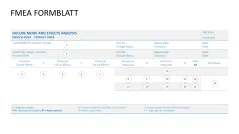
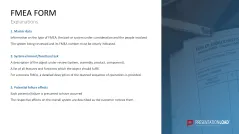
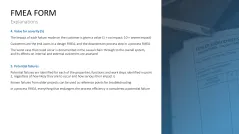
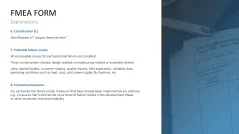
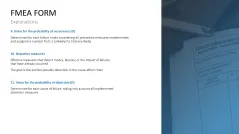
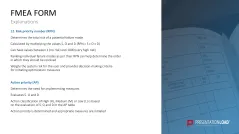
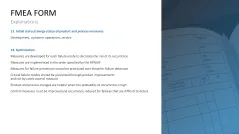
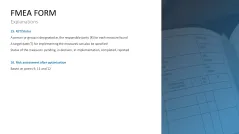
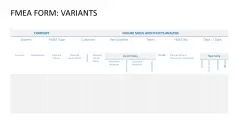
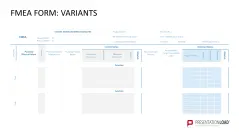
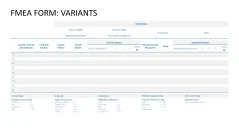
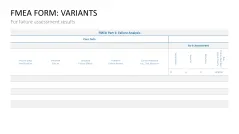
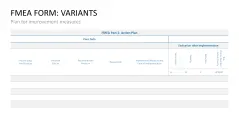